DC Drive to AC Drive Conversion
AC motors (or brushless DC, AC vector drive) can be applied to improve the process and solve any maintenance or operation issues since DC motors are not suitable in unclean environment, are less performance than AC and must be maintained on regular bases. However, conversion and controls can be extremely difficult (I can say impossible for you to design ALONE) unless you come across the same application already made valid by your supplier showing many years in operation and it is impossible for anyone to start the project ALONE if the same application (retrofit was) was not already done in the past.
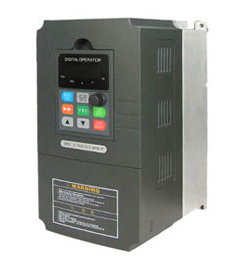
For extruder applications, AC are starting to replace DC motors but you have many variables to consider in extruder application (not only motor and drive conversion) and controlling all the variables and this project can turn extremely complex for you to solve if you do not have already an application.
One example or weakness of the AC drive is sized. AC drives will generally always be larger than DC drives by a factor of 1.5 - 2:1. In order to produce adjustable frequency current, first you must rectify the AC line to a DC bus (a DC drive) and then rectify that bus back into variable frequency.
Therefore, there are twice as many power components in an AC drive as in a DC drive. In the past, the regulator has been approximately twice as complex as that of a DC drive. Present with digital technology or state-of-the-art electronics allows this factor of complexity to come much closer to 1:1 than 2:1. Circuits that were difficult to produce with discrete parts can now be accomplished with large scale chips and microprocessors. This has greatly reduced the complexity differences between AC drives and DC drives.
In summary, conversion of DC to AC is possible but hard to achieve if you can not have your manufacturer or drive supplier provide you already with some similar or identical application. You need to get the answer from him but the project has to be a viable option (cost) for you also! The conversion will be very expensive compare to staying with DC (existing or brushless). However, if you can improve your production, process etc... in the long run, it will be a good choice.
So you need to figure out if it is possible to convert and carefully go thru the design stages (if you do not have already an existing application). Custom design can cost you a lot of money! Maybe not possible if you can not justify the cost.
One important reason is the important trend in industry today, is that of control integration. Control integration is the successful combination of drive control, process control, machine control, and operator control. I am sure you have pressure, temperature and other important variables other than speed or speed range to monitor and control at different stages in your process and the first task will be to a arrange a meeting with the different disciplines and manufacturers (you are not the only engineer to be blamed later on! if you encounter some difficulties in your project). As each one of the controls and functions is complex and automated, it is important to consider the overall architecture of your machine or process with AC. How those control elements interact with each other will determine how reliable, powerful and cost effective the CONVERSION from DC to AC will be.
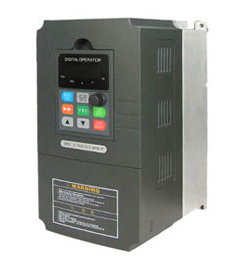
For extruder applications, AC are starting to replace DC motors but you have many variables to consider in extruder application (not only motor and drive conversion) and controlling all the variables and this project can turn extremely complex for you to solve if you do not have already an application.
One example or weakness of the AC drive is sized. AC drives will generally always be larger than DC drives by a factor of 1.5 - 2:1. In order to produce adjustable frequency current, first you must rectify the AC line to a DC bus (a DC drive) and then rectify that bus back into variable frequency.
Therefore, there are twice as many power components in an AC drive as in a DC drive. In the past, the regulator has been approximately twice as complex as that of a DC drive. Present with digital technology or state-of-the-art electronics allows this factor of complexity to come much closer to 1:1 than 2:1. Circuits that were difficult to produce with discrete parts can now be accomplished with large scale chips and microprocessors. This has greatly reduced the complexity differences between AC drives and DC drives.
In summary, conversion of DC to AC is possible but hard to achieve if you can not have your manufacturer or drive supplier provide you already with some similar or identical application. You need to get the answer from him but the project has to be a viable option (cost) for you also! The conversion will be very expensive compare to staying with DC (existing or brushless). However, if you can improve your production, process etc... in the long run, it will be a good choice.
So you need to figure out if it is possible to convert and carefully go thru the design stages (if you do not have already an existing application). Custom design can cost you a lot of money! Maybe not possible if you can not justify the cost.
One important reason is the important trend in industry today, is that of control integration. Control integration is the successful combination of drive control, process control, machine control, and operator control. I am sure you have pressure, temperature and other important variables other than speed or speed range to monitor and control at different stages in your process and the first task will be to a arrange a meeting with the different disciplines and manufacturers (you are not the only engineer to be blamed later on! if you encounter some difficulties in your project). As each one of the controls and functions is complex and automated, it is important to consider the overall architecture of your machine or process with AC. How those control elements interact with each other will determine how reliable, powerful and cost effective the CONVERSION from DC to AC will be.